Anti-Foam Control Solutions-- Efficient Solutions for Foam Reduction in Manufacturing
Exactly How Anti-Foam Control Solutions Enhance Product Top Quality and Effectiveness
The function of anti-foam control options in commercial procedures can not be overemphasized, as they are essential in boosting both item top quality and functional effectiveness. By properly mitigating foam development, these options not just make sure constant product structure across various industries but also minimize the risk of contamination, which is essential for maintaining high pureness criteria.
Recognizing Foam Development
Foam formation is a common phenomenon run into in numerous commercial processes, frequently resulting from the communication of fluids with gases or solids. This phenomenon takes place because of the stabilization of gas bubbles within a liquid matrix, bring about the production of a frothy layer externally. The visibility of surfactants, which lower the surface area tension of fluids, can worsen foam formation by facilitating bubble development and stabilization.
Several variables influence foam development, consisting of the nature of the liquid, the visibility of pollutants, temperature, and frustration levels. High shear pressures during blending can introduce more air right into the liquid, promoting bubble development. Furthermore, hydrophilic and hydrophobic materials can engage with fluid surfaces, influencing bubble stability.
Recognizing the mechanisms of foam development is important for sectors such as food processing, drugs, and petrochemicals, where foam can hinder production effectiveness and alter product quality. Identifying the details conditions that cause foam generation allows for far better layout and control of processes, ultimately causing boosted operational results. Recognizing these fundamental aspects of foam formation sets the stage for checking out effective options to mitigate its unfavorable effects in commercial applications.
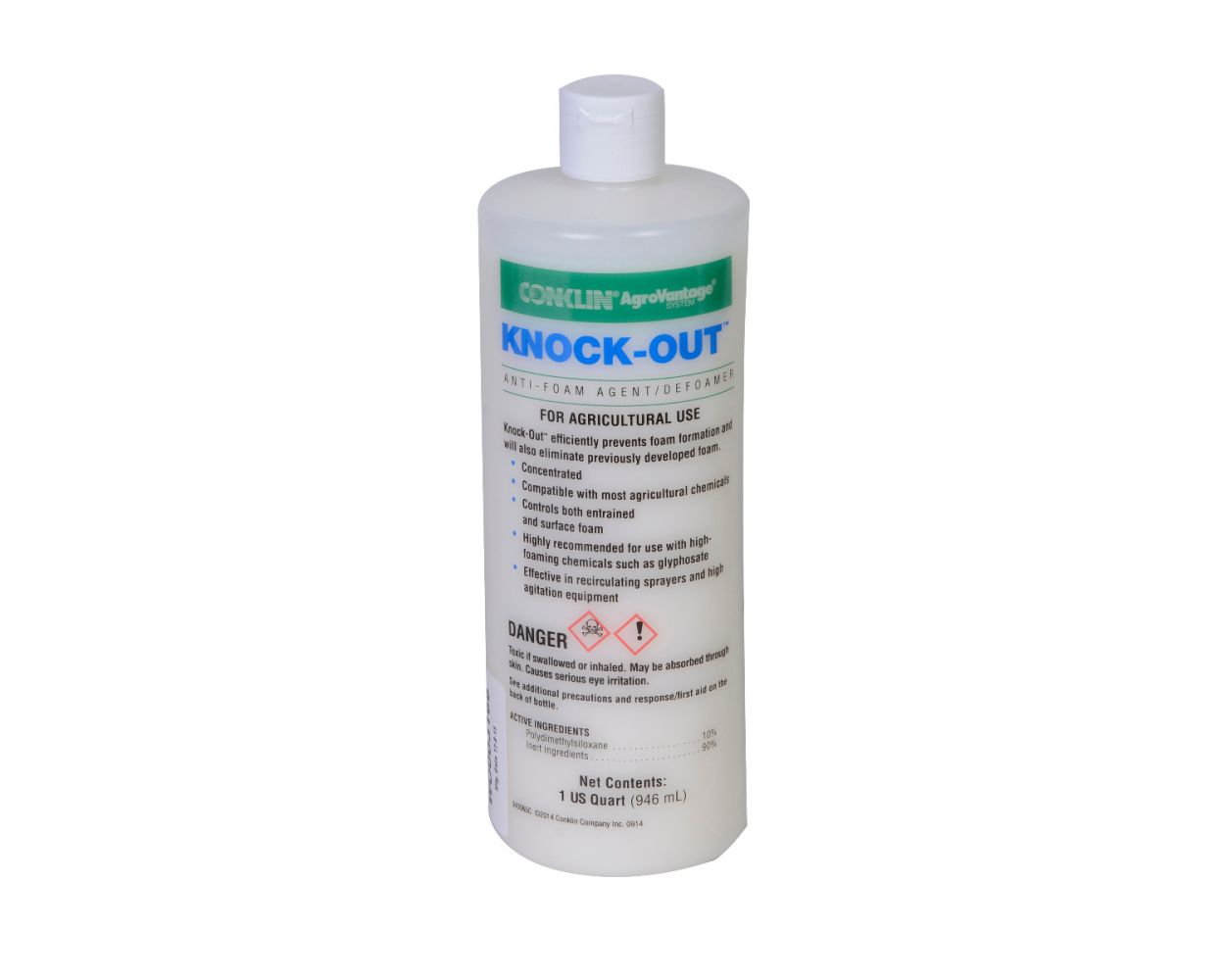
Relevance of Anti-Foam Solutions
While foam formation can improve particular processes, its unplanned visibility commonly leads to substantial operational difficulties across various markets. In production, for instance, too much foam can prevent the accurate dimension of fluids, leading to variances in item formula.

The significance of anti-foam solutions extends past operational effectiveness; they also play an essential function in keeping safety standards. In sectors such as food and drink processing, where hygiene is vital, controlling foam can prevent contamination threats related to overflow and splilling. Ultimately, the application of anti-foam solutions is important for enhancing production procedures, guarding tools, and making certain compliance with sector laws. Their function is crucial in advertising overall functional quality across diverse fields.
Benefits to Item High Quality
Reliable anti-foam remedies substantially improve item high quality throughout various sectors by ensuring regular solution and stopping the introduction of impurities. The existence of foam during production procedures can bring about irregularity in product attributes, which eventually affects completion user's experience. By mitigating foam formation, these remedies facilitate uniform blending and diffusion of components, causing a product Web Site that fulfills rigorous quality standards.
Furthermore, anti-foam representatives aid keep ideal thickness and appearance, which are critical for products such as layers, food, and pharmaceuticals. Anti-Foam Control Solutions. A stable formulation is not just visually appealing yet also functionally premium, guaranteeing that items carry out as intended. Furthermore, the reduction of foam minimizes the danger of contamination, as trapped air can present undesirable bacteria or international fragments that compromise product honesty
In applications like fermentation or chemical reactions, reliable anti-foam services sustain optimal yield and item uniformity, which are vital for keeping brand track record and customer contentment. By prioritizing product top visit their website quality, manufacturers can promote depend on and commitment among consumers, eventually adding to long-term success in the marketplace.
Enhancing Operational Performance
A significant reduction in foam can result in improved functional performance in manufacturing processes throughout numerous industries. When foam is minimized, it enables smoother operations, consequently reducing downtime connected with foam-related concerns. Too much foam can create overflow, disrupt equipment functionality, and necessitate regular maintenance interventions, all of which contribute to ineffectiveness and boosted functional prices.
By implementing efficient anti-foam control solutions, makers can streamline their processes, causing improved throughput and efficiency. The decrease of foam helps with far better mixing and reaction times in chemical procedures, which is crucial in markets such as food manufacturing, pharmaceuticals, and wastewater treatment. With a more stable process setting, suppliers can accomplish extra consistent item outcome, consequently boosting overall operational reliability.
Furthermore, boosted functional efficiency can lead to cost savings in raw products and power usage. When foam is regulated properly, sources are utilized better, leading to a decrease in waste and functional prices. Companies are much better positioned to meet production targets and react to market needs promptly, eventually contributing to a stronger competitive benefit in the market.
Choosing the Right Anti-Foam Agent
Selecting the appropriate anti-foam representative is crucial for sustaining the operational effectiveness gotten with efficient foam control. The choice of representative can dramatically affect both the performance of the procedure and the top quality of the end product. Variables such as the nature of the foam, the handling atmosphere, and the specific application has to be taken into consideration to make sure optimal outcomes.
Anti-foam agents can be categorized right into two key types: silicone-based and non-silicone-based. Silicone agents are recognized for their exceptional effectiveness in high-shear and high-temperature applications, while non-silicone agents might be liked in industries such as food and beverage as a result of regulative factors to consider. It is vital to assess the compatibility of the anti-foam representative with the materials and processes included.
Additionally, the concentration of the anti-foam agent plays a vital function; excessive usage can cause negative influence on item high quality, while not enough quantities might fail to manage foam sufficiently. Performing complete testing and pilot tests can assist determine one of the most suitable anti-foam agent for a particular application, inevitably enhancing both product quality and functional performance.
Verdict
Finally, anti-foam control services play an essential function in Read More Here boosting product quality and operational performance across different markets. Anti-Foam Control Solutions. By minimizing foam development, these options guarantee regular blending and product texture while minimizing contamination dangers. The resultant smoother procedures add to minimized downtime and boosted throughput, thereby enhancing resource application and improving overall manufacturing targets. The selection of appropriate anti-foam representatives additionally magnifies these advantages, strengthening their relevance in industrial applications.
By effectively mitigating foam formation, these services not just guarantee consistent product appearance throughout numerous markets but likewise lessen the risk of contamination, which is important for maintaining high pureness requirements.Recognizing the devices of foam development is important for sectors such as food processing, pharmaceuticals, and petrochemicals, where foam can impede production effectiveness and modify item quality. The existence of foam throughout production processes can lead to variability in item features, which eventually impacts the end user's experience. By reducing foam formation, these options help with consistent blending and dispersion of components, resulting in a product that meets stringent top quality criteria.
Picking the appropriate anti-foam agent is crucial for sustaining the operational efficiency gained via reliable foam control.